Wind Turbine Repair & Servicing
Our highly experienced service and repair technicians are committed to meeting the demands of your wind turbine equipment 24/7.
Your partner in performance and reliability
Call Back Form
Complete the form below and one of our friendly team members will be in touch to discuss your requirements. For even faster response, please phone us at any time during business hours.
At EMACS, we deliver end-to-end electrical and mechanical servicing solutions for wind turbines across Australia. With specialist capabilities in workshop and onsite repair, diagnostics, and overhauls, our team ensures your wind assets run efficiently, reliably, and safely.
Whether you operate a single turbine or manage a full-scale wind farm, we’re ready to respond—with rapid turnaround and industry-leading expertise.
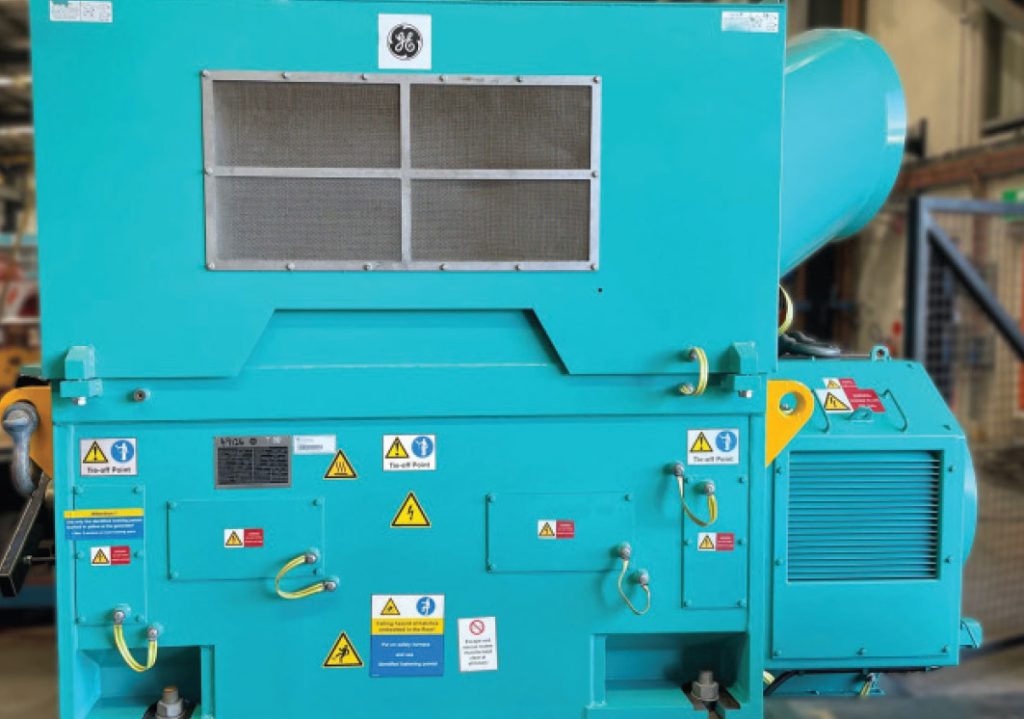
Electrical Services
We perform complete overhauls of wind turbine generators and alternators, restoring performance and extending asset life. Our service includes disassembly, inspection, repair, reassembly, and full electrical testing.
Our precision rewinding capabilities cover high and low voltage stators and rotors. We handle everything from insulation upgrades to full rewinds, using materials rated for extreme operational conditions.
All overhauled equipment is subject to rigorous load testing using our in-house facilities, simulating real-world electrical loads to verify performance, durability, and safety.
We specialise in the repair and replacement of pitch and yaw motors—critical for blade control and turbine positioning—as well as cooling motors for optimal thermal performance.
From compact auxiliary systems to large-scale utility turbines, our workshop and field teams are equipped to handle projects ranging from 1kW up to 50MW.
We maintain a wide inventory of spare parts, including windings, bearings, slip rings, brushes, and motor components—minimising downtime and ensuring fast replacements.
Mechanical Services
Our team overhauls wind turbine gearboxes to OEM standards, restoring gear meshing, inspecting bearings, and replacing worn components to eliminate vibration and noise issues.
We can help to extend the life of critical assets by restoring worn or damaged parts to original specifications—or improving them for enhanced performance. Using precision machining and advanced diagnostic tools, we accurately replicate or redesign components that are no longer supported by OEMs, reducing downtime and providing a cost-effective alternative to replacement.
We conduct detailed oil sampling and lubricant analysis to detect contamination, wear particles, and fluid degradation—helping you plan maintenance before failure occurs.
Precision dynamic balancing reduces vibration and extends equipment life. Our balancing capability accommodates rotating assemblies up to 20 tonnes.
We repair or replace slip rings and associated components to ensure reliable electrical continuity between rotating and stationary parts—reducing electrical noise and overheating risks.
Heavy-duty machining services for large wind turbine components are handled in-house, with capacity for parts up to 15 tonnes.
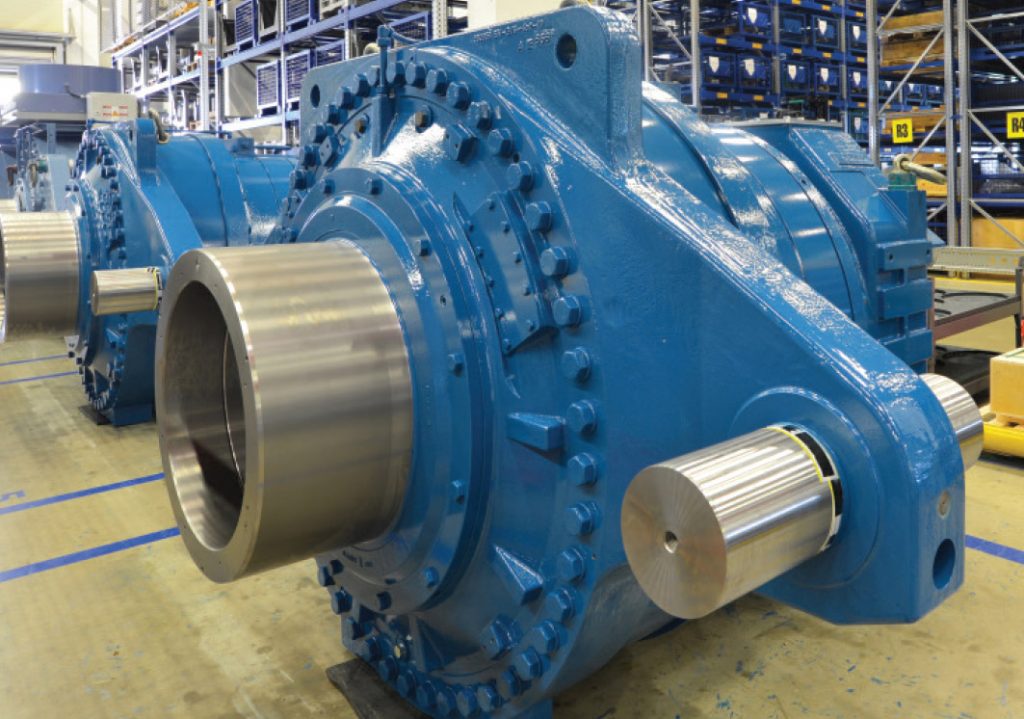
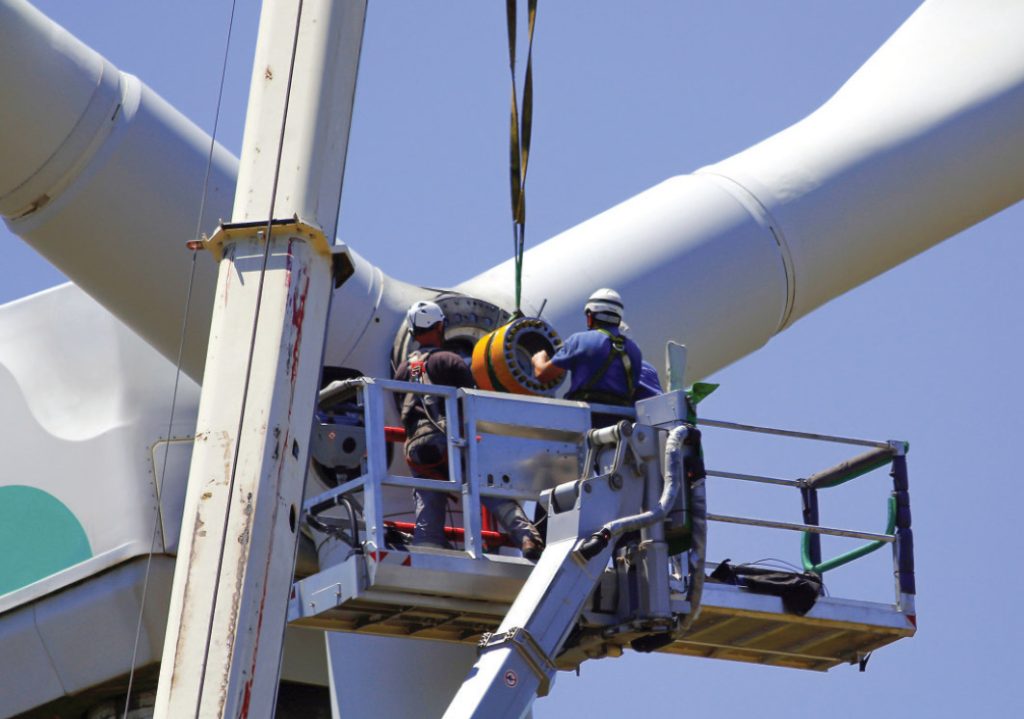
Onsite Services
Our field teams perform onsite HV testing including insulation resistance, surge comparison, and partial discharge testing, identifying issues early to prevent major failures.
Non-invasive borescope inspections allow us to visually assess internal gearbox components and provide detailed reporting—ideal for condition monitoring and maintenance planning.
Avoid costly crane hire and downtime—our technicians perform up-tower bearing replacements quickly and safely, using specialised tooling and rigging.
Precision alignment and condition monitoring services are offered to optimise rotating equipment performance. Vibration trends and thermal imaging help identify alignment faults, imbalance, and overheating.
Routine cleaning, reconditioning, and replacement of slip rings and brushes reduces electrical arcing, improves reliability, and extends component life.
FAQs
Breakdowns don’t wait—and neither do we. EMACS offers around-the-clock emergency repair services, both onsite and in our workshop. Our rapid response teams are ready to minimise your downtime and restore operations quickly, safely, and reliably.
Yes. Our team has experience across a wide range of wind turbine brands, including GE, Vestas, Siemens Gamesa, Goldwind, and more. We tailor each service to the manufacturer’s specifications and site conditions.
Absolutely. Our field technicians are trained and equipped to carry out up-tower bearing replacements, slip ring maintenance, and other critical repairs without the need for costly crane hire—saving you time and expense.
Our workshop can handle rotating equipment up to 50MW and machining up to 15 tonnes. We also offer dynamic balancing for components up to 20 tonnes, making EMACS one of the most capable service providers in the region.
Yes. Our onsite services include high-voltage generator testing, gearbox borescope inspections, vibration analysis, thermal imaging, and laser alignment. These tools help detect faults early and support condition-based maintenance planning.
Yes. We supply a wide range of genuine and aftermarket spare parts, including slip rings, brushes, bearings, insulation materials, and motor components—backed by expert advice to ensure compatibility and reliability.
You can phone us directly on 61 7 3271 5599, or request a quote using our online form.
One of our specialists will be in touch to discuss your needs and schedule a site visit or workshop service.